Übergroße Kunststoffteile additiv zu fertigen bietet enorme Vorteile für die werkzeuglose Herstellung kleiner und mittlerer Serien. Ein Schlüssel dazu ist das VFGF-Verfahren (Variable Fused Granulate Fabrication), ein Extrusionsverfahren, das Q.Big 3D entwickelt hat. Es ist unter anderem dazu geeignet, modular aufgebaute Cockpits für Flugfeld-Simulatoren additiv zu fertigen.
Autor: Guido Radig, freier Fachredakteur, Weichs
Inhaltsverzeichnis
1. Das VFGF-Verfahren in der Anwendung – Entwicklungsprojekt 3D-Cockpit
2. 3D-Drucker Queen 1 für das VFGF-Verfahren
3. Der Anbieter – Q.Big 3D
Das VFGF-Verfahren (Variable Fused Granular Fabrication) ermöglicht die Herstellung großvolumiger 3D-Bauteile aus Kunststoffgranulaten. Charakteristisch für dieses 3D-Extrusionsverfahren ist die Fähigkeit, einen variablen Düsendurchmesser zu verwenden. Das VFGF-Verfahren ermöglicht es, präzise und hochauflösend an Stellen zu drucken, an denen feine Details erforderlich sind, wie beispielsweise an den Außenflächen eines Bauteils.
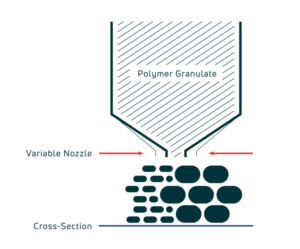
Bild: Q.Big 3D GmbH, Aalen
Gleichzeitig können innenliegende Strukturen oder Bereiche, bei denen die Auflösung weniger relevant ist, in einem sogenannten Turbomodus grob und damit schneller gedruckt werden. Diese Flexibilität des Verfahrens erlaubt daher hohe Aufbaugeschwindigkeiten der 3D-Bauteile. Durch angepasste Prozessalgorithmen (Predictive Flow Algorithmus) bietet das Verfahren einen Bauteilaufbau zur rechten Zeit, an der richtigen Stelle, mit der richtigen Menge Material. Dadurch ist es möglich, auch komplexe Bauteile mit Hinterschnitten mithilfe von Stützfunktionen, zu drucken.
Der 3D-Druck mit marktgängigem Kunststoffgranulat ohne Filamente ermöglicht es, technische Kunststoffe mit seriennahen Eigenschaften zu sehr günstigen Stückkosten zu verarbeiten. Durch das Aufschmelzen in einem speziell entwickelten Schneckenextruder können höhere Durchsätze ermöglicht werden, wodurch die Druckdauer signifikant reduziert wird. Zusätzlich lassen sich fasergefüllte Materialien mit hoher Dimensionsstabilität, sowie elastische Materialien drucken.
Die werkzeuglose Fertigung mit einem Extrusions-3D-Drucker eröffnet Anwendern zeitnahe Time-to-Market-Strategien. Der Entfall der Werkzeugkosten und neue Strategien der Bauteil-Geometrie in der Konstruktion treffen auf extrem kurze Amortisationszeit der Anlagentechnik. Der besondere Clou gegenüber alternativen AM-Strategien, wie FDM-3D-Drucker, ist der Einsatz von handelsüblichen Standard-Granulaten ohne Filamente im 3D-Druck.
Das VFGF-Verfahren in der Anwendung –
Entwicklungsprojekt 3D-Cockpit
Das Unternehmen Reiser Simulation and Training beauftragte für einen Full-Flight Simulator von Hubschraubern Murtfeldt Additive Solutions (Murtfeldt AS) mit der Fertigung eines modular aufgebauten Cockpits. Das Cockpit wurde auf einer Queen 1-Anlage von Q.Big 3D bei Murtfeldt gefertigt.
Die Wahl des Verfahrens
Zielsetzung des Entwicklungsprojektes war es, die bisherigen Limitationen konventioneller Fertigungsstrategien mit einer zeitgemäßen Lasersinter-Strategie (SLS) zu überwinden. So fallen bei klassischen formgebundenen Verfahren, insbesondere bei großvolumigen Bauteilen, hohe Werkzeugkosten verbunden mit langen Vorlaufzeiten an. Zudem können klassische FDM-3D-Drucker meist nicht großvolumige 3D-Bauteile fertigen: die Aufbauraten sind unwirtschaftlich und das Material mit Filamenten weist oft einen 7-fach höheren kg-Preis, im Vergleich zu einem Granulat-3D-Drucker, auf.
Als Lösung bot sich die AM-Fertigung auf einer Queen 1 von Q.Big 3D an, die bei Murtfeldt AS für übergroße SLS-Bauteile zu Verfügung steht. Das Cockpit mit den Maßen 2.260 mm (x), 1.780 mm (y) und 1.705 mm (z) wurde als zerlegbares Modul konzipiert, einerseits um den Aufbau beim Anwender zu erleichtern. Andererseits konnten so mit einem Conversion Kit zwei Hubschraubermodelle (Airbus Helicopters H135 und H145) kostenvorteilig abgebildet werden. Nicht zuletzt sind durch eine Segmentierung der 3D-Baugruppe Funktionsintegrationen wie integrierte Kabelkanäle möglich.

Bild: Q.Big 3D GmbH, Aalen
Vorteile des VFGF-Verfahrens
Hinzu kommen folgende Vorteile des VFGF-Verfahrens:
- Geringes Gewicht des Bauteils von nur 200 kg
- Die Beherrschung von Verzug bei diesen großen und komplexen Bauteilen,
- Enge Toleranzen der Spaltmaße
- Hohe Oberflächengüte
Gerade die Maßhaltigkeit ist für die Verschraubung und Verstiftung elementar wichtig.
Der Bauteilaufbau aller Bauteile betrug etwas über einen Monat. Für ein Folgeprojekt rechnet Murtfeldt AS durch Optimierung der Prozesskette aber mit kürzeren Aufbauzeiten. Durch ein 3D-Drucker-Netzwerk aus mehreren Queen 1-Anlagen kann die Lieferzeit für zeitkritische Anfragen ebenfalls gekürzt werden.
Material des Cockpits
Für den Rahmen des Cockpits verwendete Murtfeldt AS ein teilaromatisches Polyamid mit 25% Glasfaseranteil (Q.mid GF25). Dieses Material weist mit 0% längs und 0,2% quer einen besonders hohe Maßhaltigkeit auf, eine hohe Temperaturstabilität bis 200°C, hohe Steiffestigkeit und eine ausgezeichnete Lackierbarkeit. Q.mid GF25 ist für zahlreiche Anwendungsgebiete qualifiziert. Die fertige Cockpit-Baugruppe wird zum Abschluss in matt schwarz lackiert (Durchlaufzeit ca. zwei Wochen), damit keine störenden Lichtreflexe im Simulator entstehen.
3D-Drucker Queen 1 für das VFGF-Verfahren
Die guten Resultate des modularen 3D-Cockpits ergeben sich aus einer durchdachten Anlagentechnik: Die aktive Temperierung einer äußeren Kammer sowie des Bauraumes der Queen 1 ermöglich einen stabilen und wiederholgenauen Prozess, da die Temperaturen nicht nur des Bauraums sondern auch der gesamten Mechanik, unabhängig von Temperaturschwankungen in der Produktionshalle konstant gehalten werden können.
Das Besondere ist die variable Düse des 3D-Druckers. Für die schnellen Aufbauraten der Queen 1 sorgt eine variable Düsenansteuerung, die an die Besonderheiten jeder Geometrie angepasst wird:
- Filigrane Bereiche der Bauteile werden im normalen Modus der Düse aufgebaut.
- Flächige Infill-Bereiche an den dicken Holmen des Cockpits hingegen werden im schnellen Turbo-Modus aufgebaut, um die Fertigungsdauer bei gleichzeitig höherer Stabilität zu reduzieren.
Den Wechsel der Modi realisiert die Queen 1 automatisch. Konstruktiv gab Reiser für die Düsenansteuerung sensible Bereiche vor: An den Anschraubpunkten der Türscharniere beispielsweise wurde Vollmaterial vorgegeben. Dies ermöglicht eine stark verkürzte Fertigungszeit gegenüber einem durchgängigen Düseneinsatz, sowie einen materialsparenden Leichtbau der 3D-Bauteile.
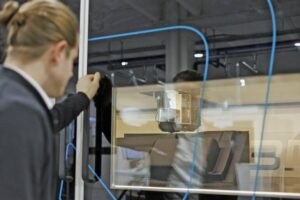
Bild: Q.Big 3D GmbH, Aalen
Johannes Matheis, Geschäftsführer bei Murtfeldt AS: „Mit dem VFGF-Verfahren von Q.Big 3D für großvolumige 3D-Bauteile können wir bei Murtfeldt AS gezielt weitere Anwendungsgebiete für die SLS-Fertigungsstrategie erschließen. Wenn man die gesamte Prozesskette beherrscht, sind komplexe, große 3D-Bauteile mit hoher Wiederholgenauigkeit und Bauteilgüte auf einem neuen Niveau möglich.“ (eve)
Der Anbieter – Q.Big 3D
Die Q.Big 3D GmbH, mit Sitz in Aalen (Deutschland), ist ein Start-up des 3D-Anlagenbaus, gegründet im Jahre 2019 von Dennis und Katja Herrmann als Absolventen der Hochschule Aalen. Das Unternehmen ist strategischer Partner der Manz AG (Reutlingen) und der HZG-Gruppe (Coburg) als Investor.
Startup Q.Big 3D erhält 2 Millionen Euro als Serie A-Finanzierung
Die 3D-Drucktechnik von Q.Big 3D ermöglicht die Herstellung großvolumiger 3D-Bauteile ( 200 kg) auf Basis des Einsatzes von handelsüblichen Kunststoffgranulaten ohne Filamente (wie PP, PA, ABS, TPE, TPU, PLA mit GF-Füllgraden bis 25 %). Grundlage bildet das VFGF-Verfahren, ein 3D-Extrusionsverfahren, welches hohe Präzision mit hohen Aufbaugeschwindigkeiten vereint. Die Anlage Queen 1 bietet einen Bauraum von Breite 1.700 mm / Höhe 1.050 mm / Tiefe 1.050 mm. Die Verfahrensgeschwindigkeit liegt bei max. 500 mm/s. Die Anlage ermöglicht eine dynamische Ausstoßmenge 0,15 – 2,0 kg/h.
Die Anwendungen reichen von Funktions- und Struktur-Bauteilen für den Anlagen- und Maschinenbau, über den Automobilsektor für Nutzfahrzeuge und Landmaschinen, Tanklösungen, Energietechnik bis hin zu ergonomischen und medizintechnischen Produkten.
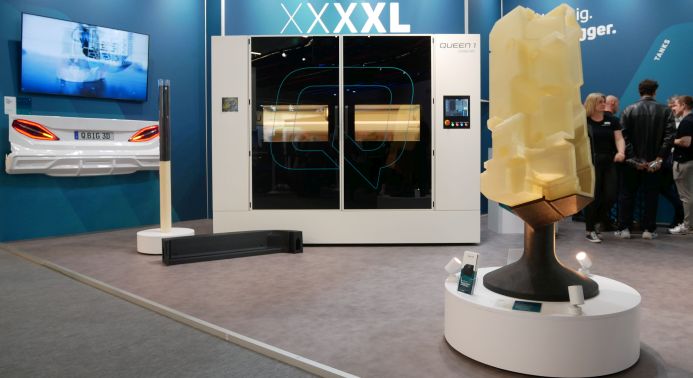
Das Team bietet neben der Anlagentechnik Dienstleistungen zur Unterstützung von Anwendern an. Dazu zählen Designberatung, prozessoptimiertes Slicing, anwendungstechnische Unterstützung, Optimierung der Nachbearbeitung im Post-Processing, Anlagenschulung und Aufgabenstellungen der Qualitätssicherung.
Messe Formnext 2024: Halle 11.1, Stand E 19