Mit einer Mischung aus Neugier und praktischem Engagement haben die beiden Studenten Zachary Lesan und Patrick Watson vom Studiengang Luft- und Raumfahrttechnik der Universität Colorado (CU) ein unabhängiges Projekt zur Entwicklung und Herstellung von Turbopumpen für Flüssigkeitsantriebe gestartet. Aufgrund des Laser-Powder-Bed-Fusion-Verfahrens, gelang es den beiden, diese Raumfahrtkomponente wirtschaftlicher und skalierbarer herzustellen.
Inhaltsverzeichnis
1. Raumfahrttechnik wird durch 3D-Druck wirtschaftlicher
2. Velo3D bietet Technologie und Dienstleistungen für das Projekt
3. Additive Fertigung prägt das Design der Turbopumpe
4. Minimierung der Teilezahl – Minimierung der Fehlerquellen
5. 3D-gedrucktes Bauteil reduziert Leckageverluste
6. Die Velo3D Sapphire-Drucker
7. Ein Projekt gelingt nur mit den richtigen Partnern
In den letzten fünf Jahren wurden in der Raumfahrt- und Raketentechnologie aufgrund des 3D-Drucks enorme Fortschritte erzielt. Sowohl unabhängige Ingenieure als auch kommerzielle Unternehmen arbeiten an einteiligen Raketenkonstruktionen und konsolidierten Fertigungsverfahren. Ziel ist es, weniger auf maschinelle Bearbeitung, Gießen, Löten und traditionelle Fügetechniken zurückzugreifen, die die funktionale Leistung einschränken, die Zuverlässigkeit verringern und von einer schrumpfenden Lieferkette stammen.
Raumfahrttechnik wird durch 3D-Druck wirtschaftlicher
„Viele Unternehmen gießen ihre Teile“, sagt Patrick Watson. „Der wirklich große Durchbruch bei Turbomaschinen für die Raumfahrt oder den Energiesektor ist der Metall-3D-Druck, vor allem das Laser Powder Bed Fusion (LBPF). Wir können jetzt die gewünschten Leistungsgeometrien drucken, die Designs iterieren, die benötigten Oberflächen erhalten und die Bearbeitung gezielter einsetzen.“ Der 3D-Druck von Metall habe das Projekt erst möglich gemacht.
Das akademische Ziel des Reaper-Triebwerks (benannt nach einer scharfen Paprika aus South Carolina), eines Flüssigkeitsantriebs, war die Erforschung flexibler und wirtschaftlicherer Methoden zur Herstellung von Raketen. Sowohl Zachary Lesan als auch Patrick Watson waren sich darüber im Klaren, dass der Erfolg dieses Projekts von der Senkung der Kosten für die Raumfahrt abhängen.
Velo3D bietet Technologie und Dienstleistungen für das Projekt
Die schwierigste, aber vielleicht lohnendste Aufgabe des Projektes bestand darin, Kooperationspartner aus der Industrie zu finden, die 3D-Druck, maschinelle Bearbeitung, Standardteile wie Dichtungen und Befestigungselemente sowie Beratung anbieten konnten. Lesan und Watson machten die Akquisition von Partnerschaften zu einem wichtigen Element bei der Verlagerung von Unterstützung und Produktion über das schulische Fertigungslabor hinaus zu fortschrittlicheren Industriestandorten.
Mit dem Ziel der Einzelteilkonstruktion ging Lesan schon früh online und kontaktierte den Metall-AM-Anbieter Velo3D über die Website des Unternehmens. Er wusste, dass deren fortschrittliche Laser-Powder-Bed-Fusion (LPBF)-Druckmöglichkeiten für die Produktion des SpaceX Raptor-Triebwerks von zentraler Bedeutung waren. Diese Online-Anfrage führte zu einem Gespräch mit Zach Murphree, VP of Global Sales and Business Development von Velo3D, und Gene Miller, Director of Technical Sales. Beide ermutigten Lesan und boten die Technologie und Dienstleistungen des Unternehmens für das Projekt an.
„Murphree und Miller waren von dem Projekt begeistert“, so Lesan. „Und ihre Begeisterung hat mich noch mehr motiviert. Die Konstruktionsmöglichkeiten der Velo3D-Drucker und ihre persönliche Ermutigung haben mich schließlich dazu gebracht, den gesamten Konstruktionsprozess der Turbopumpe zu durchlaufen.“
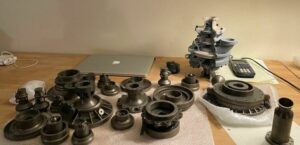
Bild: Patrick Watson
Additive Fertigung prägt das Design der Turbopumpe
Da er sich bereits als Teenager mit Festkörperraketen beschäftigt hatte und seit den 1960er Jahren über zahlreiche Daten zu Turbopumpen verfügte, hatte Lesan die Grundlagen für die Konstruktionsarbeit, die er an der CU Boulder durchführen sollte. Nun musste er sein eigenes MethaLOX-Modell (Methalox = Triebwerk, das mit flüssigem Wasserstoff und Flüssigsauerstoff angetrieben wird; Anm. d. Red.) entwickeln. Das Modell sollte die Vorteile des LPBF-Verfahrens nutzen.
Turbopumpen sind ein bekanntes Phänomen. Lesan rechnete nicht damit, ihre Leistung zu verbessern, aber vielleicht konnten er und Watson durch additive Fertigung die Kosten senken und die Zuverlässigkeit gegenüber bestehenden Systemen erhöhen.
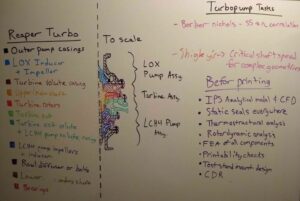
Bild: Zachary Lesan
Minimierung der Teilezahl – Minimierung der Fehlerquellen
Die Konsolidierung von Teilen dient der Qualitätsverbesserung, da die Dichtungsschnittstellen der Komponenten, eine historische Fehlerquelle, eliminiert werden. Turbopumpen sind seit langem auf Dichtungen angewiesen, um ihre Abschnitte zu verbinden. Trotz generationenübergreifender Fortschritte sind Dichtungen angesichts der hohen Flüssigkeits-/Gasdrücke in den Pumpen- und Turbineneinheiten immer noch ein Risikobereich.
„Wir haben durch die Minimierung der Teilezahl so viele potenzielle traditionelle Fehlerquellen beseitigt“, sagt Lesan. „Das Problem bei additiver Fertigung ist die Porosität und die Überprüfung der Teile. Wir können uns unsere Bauberichte ansehen und sehen, dass es keine Fehler im Prozess gab, die die Qualität beeinträchtigen.“
3D-gedrucktes Bauteil reduziert Leckageverluste
„Es gibt einige Teile, die wir kaufen oder konventionell herstellen mussten“, sagt Watson. „Bei den gekauften Teilen handelt es sich um Armaturen, Lager, Dichtungen und Verbindungselemente zum Verbinden von Flanschabschnitten. Aber ansonsten lag der Schwerpunkt auf der Schaffung eines arbeitsfreundlichen, kostengünstigeren Systems, das die traditionellen Passungsprobleme durch kombinierte Teile vermeidet. Es gibt hier auch einen Sicherheitsaspekt“, bemerkt Watson. „Die inneren Antriebsdichtungen, die aus einem Teil bestehen, entsprechen nicht der Norm. Durch die Verwendung eines Stickstoff-Spülsystems, das in die Reaper-Turbopumpengehäuse integriert ist, können wir die Gefahr einer Vermischung der Treibstoffe und damit eines katastrophalen Versagens effektiv ausschließen. Wir sind in der Lage, Leckageverluste zu reduzieren, Leistungsprobleme und sogar Explosionen zu vermeiden. Ein einziges AM-produziertes Teil, das sich auf schwierige Überhangwinkel und Ansätze stützt, erreicht dieses Ziel.“
Sid Raje, Velo3D Business Development Account Manager: „Lesan und Watson haben darauf aufgebaut, wohin sich die Industrie mit Flüssigsauerstoff- und Methanantrieb bewegt, aber das Ausmaß ihres Einsatzes von Advanced AM für die Konsolidierung von Teilen und anspruchsvollen Geometrien, Oberflächen und Überhängen sticht wirklich hervor. Die Senkung der Nachbearbeitungskosten und die verbesserte Systemzuverlässigkeit sind Wissen, das sie und andere weiterführen werden.“ (eve)
Die Velo3D Sapphire-Drucker
Im Gegensatz zu herkömmlichen AM-Druckern verfügen die Sapphire-Drucker über einen überstandstoleranten, berührungslosen Recoater, der urheberrechtlich geschützt ist. Dieser Recoater schließt das Risiko von Teilekollisionen nahezu aus, verbessert die Druckerleistung auf drastische Weise und ermöglicht das Drucken geringer Winkel und Überhänge mit bis zu null Grad sowie dünner, dichter Wände, großer Durchmesser und extrem kleiner Innenrohre mit wenig bis gar keinen Stützelementen.
Ein Projekt gelingt nur mit den richtigen Partnern
Lesan und Watson wurden auf ihrem schnellen Weg zur Raketenentwicklung von vielen unterstützt, die ihre Leidenschaft für die Raumfahrt teilen.
- Aus dem Bolder Aerospace Programm der CU waren dies Professor John Farnsworth sowie Cameron Micksch und Paul Wingrove aus dem Bearbeitungslabor der Universität.
- Das zweiköpfige Kernteam führte den Metall-3D-Druck mit Velo3D durch.
- Es nutzte Konstruktionssoftware und die fortlaufende Unterstützung von CFturbo sowie die Bearbeitungsdienste von Silicon Valley Elite Manufacturing und EMP.
- Sie erhielten außerdem Dichtungen von Gallagher Fluid Seals und Messgeräte von Kulite und Omega.
- Ratschläge erhielten sie informell von einzelnen Ingenieuren ihrer beiden Praktikumsunternehmen SpaceX und Launcher sowie von Ursa Major und Andrew Mitchell, früher bei Masten Space Systems, jetzt Astrobotic.