Vor 18 Monaten begann Atlas Copco ein Sprintprojekt, um neue Marktchancen in Bereichen wie Elektrofahrzeuge zu nutzen. Man holte sich für den Bereich Industriewerkzeuge, Füge- und Fertigungstechnik die additive Fertigung in Form von Technologie von EOS ins Haus. Der Wechsel zum hauseigenen 3D-Druck hat dazu geführt, dass Atlas Copco weniger Komponenten von Drittanbietern benötigt und nicht mehr durch Werkstoff- und Transportverzögerungen in der Lieferkette eingeschränkt ist.
Inhaltsverzeichnis
1. Alle Bedürfnisse berücksichtigt
2. 3D-Drucker der Wahl: EOS P 396
3. Produktionskosten um 30 % gesenkt
4. Schnelles Produktdesign und Prototyping
Atlas Copco stellt pfiffige Technologien, Produkte und Lösungen für viele Branchen, einschließlich der Automobilindustrie bereit. Es entwirft und produziert über 70 Arten von selbstdurchdringenden Nieten, zugehörigem Werkzeug und Ausrüstung für eine Reihe von Automobilhersteller. Um flexibler reagieren zu können und die Vorlaufzeiten für die Kunden zu verkürzen, setzte man für einige Komponenten auf die polymerbasierte Additive Fertigung.
„Wir wollten eine strengere Kontrolle über unsere Fertigung, die zu kürzeren Lieferzeiten, niedrigeren Kosten und der Fähigkeit, neue Produkte schnell zu prototypisieren, führen würde“, sagt Jason Edwards, technischer Leiter Atlas Copco. „EOS und Additive Minds haben uns zu einer schlüsselfertige Lösung gebracht und uns geholfen, unsere Prozesse so anzupassen, dass wir jetzt in der Serienproduktion mit mehreren Komponenten sind, Hunderte Prototypen schnell herstellen und in nur 18 Monaten einen ROI erzielt haben.“
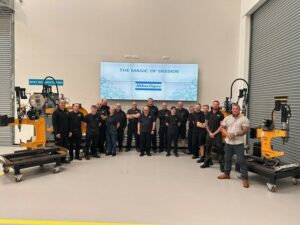
Bild: Atlas Copco
Alle Bedürfnisse berücksichtigt
EOS und Additive Minds wurden früh für das Projekt ausgewählt und arbeiteten eng mit dem Team von Atlas Copco zusammen. Entstanden ist ein Rund-Um-Glücklich-Paket jenseits der physischen Maschine – einschließlich Kosten-pro-Teile-Analyse und Datenaufbereitung. Es wurde über die besten Maschinen und Arbeitsabläufe beraten, um die aktuellen und zukünftigen Bedürfnisse von Atlas Copco mit einzubeziehen, einschließlich Pulverauswahl, Farb-, Designtransfer- und Nachbearbeitungstechniken.
Das EOS Partnernetzwerk bietet Kundenzugang zu zertifizierten Partnern, die spezielle Aspekte ihres Produktionslebenszyklus unterstützen können. Auch für alle Mitarbeiter wurden Trainingsprogramme entwickelt, die den Übergang und den Hochlauf zur polymerbasierten AM-Serienproduktion unterstützten.
3D-Drucker der Wahl: EOS P 396
Das Herz der Atlas-Copco-Lösung ist ein 3D-Drucker, der eine zuverlässige und wiederholbare hochwertige Teileproduktion gewährleistet: Der EOS P 396 , der für über eine hohe Flexibilität, hervorragende mechanische Eigenschaften und Maßhaltigkeit verfügt. Mit einer Auswahl von 14 Materialien und 26 Parametrierungs-Sets wird der Kunststoff-3D-Drucker heute die Atlas-Copco-Produktion und neue Produktdesigns bis weit in die Zukunft unterstützen. Die Maschine wurde mit einer DyeMansion DM60 Färbe-Maschine kombiniert, die über das EOS-Partnernetzwerk ausgewählt wurde. Sie ermöglicht, dass das Pulvermaterial für bestimmte Produkte gefärbt werden kann. Auf diese Weise ließe sich z. B. herausstellen, wo bestimmte Sicherheitsausrüstungen von den Bedienern von Automobilproduktionslinien verwendet werden sollten.
Produktionskosten um 30 % gesenkt
Durch die AM-Serienfertigung konnte die Komponentenproduktion beschleunigt werden, da die Lieferkette und die damit verbundenen Arbeitsstunden reduziert und Verzögerungen beim Umrüsten vermieden werden konnten. Atlas Copco konnte außerdem den Ausschuss von ca. 7 % auf nahezu Null reduzieren, was auf die Genauigkeit und Zuverlässigkeit der Komponenten zurückzuführen ist, die mit dem EOS P 396 möglich sind.
Durch die Umstellung auf den hauseigenen 3D-Druck konnte Atlas Copco die Vorlaufzeiten von 6–12 Wochen auf 3–4 Tage reduzieren und die Umweltbelastung verringern, da weniger Transporte für die Herstellung und Lieferung der Endkomponenten erforderlich sind.
Insgesamt konnten so die Produktionskosten um 30 % gesenkt werden, was Atlas Copco hilft, wettbewerbsfähiger zu sein und mehr Zeit in neue Produktinnovationen zu investieren.
Schnelles Produktdesign und Prototyping
Atlas Copco nutzt jetzt ein iteratives Prototyping-Verfahren, um sein Produktinventar zu wechseln und gleichzeitig neue Produkte zu entwickeln, mit einer Designfreiheit, die es bisher nicht erlebt hat. Das Team hat wöchentliche Treffen, um Designänderungen zu diskutieren, die dann sofort zu gedruckten Prototypen zum Testen übergehen können. AM hilft dem Team auch, die Produkte zu vereinfachen.
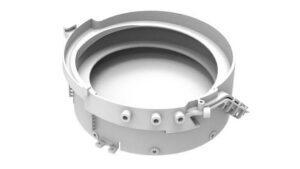
Bild: Atlas Copco
Ein Beispiel ist ein Spulenträger, der früher aus einem Gussteil bestand, das bearbeitet und montiert werden musste. Das neue Design ist nun ein einzelnes gedrucktes Bauteil, das wesentlich leichter ist und in der Herstellung weniger kostet.
„AM war für uns transformativ. Wir gewinnen neue Verträge auf der ganzen Welt, weil wir direkt, zu niedrigeren Kosten und mit kurzen Lieferzeiten liefern können. Mit EOS haben wir einen Partner, der uns während der gesamten Umstellung unterstützt hat, uns schnellen Support bietet und uns weiterhin bei der Konstruktion von Komponenten berät, um das beste Ergebnis mit unserem 3D-Drucker zu erzielen“, sagt Edwards.
„Kein Unternehmen sollte das Gefühl haben, dass es nicht zu AM wechseln kann“, sagt Nathan Rawlings, Vertriebsleiter bei EOS UK. EOS helfe den Unternehmen , durch starke Kommunikation, Zusammenarbeit und einen einheitlichen Teamgeist sicherzustellen, dass der Wechsel ein Erfolg wird. (eve)