Inhaltsverzeichnis
1. Präzisionswerkzeuge bleiben unerlässlich
2. Kreativitätsschub für neue Produkte
3. Problemlösungen zur Nachbearbeitung gefordert
Mit der 3D-Druck-Technologie kommen auch neue Zeiten auf Präzisionswerkzeuge zu. Sie ermöglicht ganz neue Lösungen, die mit herkömmlichen Fertigungsmitteln gar nicht machbar sind. Dazu gehören komplizierte Hinterschneidungen am Werkzeugkörper oder auch Freiformbohrungen für Kühlkanäle. Neben den vielfältigen Gestaltungsmöglichkeiten gibt es weitere Vorteile, wie Gewichtseinsparung durch Hohlräume und damit auch Ressourceneffizienz oder Schnelligkeit in der Bemusterung kundenindividueller Werkzeuglösungen.
Der Kreativität der Konstrukteure und auch der Fertigungstechniker sind also keine Grenzen gesetzt. Allerdings wird von ihnen auch ein komplett neues 3D-Druck-Denken gefordert. Viele bereits bestehende Produkte müssen neu konstruiert werden. Aber das sind bei weitem noch nicht alle Veränderungen, die die additive Fertigung mit sich bringt. Und über allem steht die Frage: Sind Präzisionswerkzeuge zukünftig überflüssig? Nein, sind sie nicht. Ganz im Gegenteil.
Präzisionswerkzeuge bleiben unerlässlich
Nahezu alle gedruckten Werkstücke müssen spanend nachbearbeitet werden. Die finale Oberflächenqualität reicht meistens nicht aus, auch bedingt durch den sogenannten Treppeneffekt an schrägen Wandungen, der beim für den 3D-Druck typischen Pulverbettverfahren auftritt. Dabei wird das Material pulverförmig in dünnen Schichten aufgebracht und dort, wo das Bauteil entstehen soll, per Laser geschmolzen und gesintert, Schicht um Schicht. Je dünner die Schicht ist, umso genauer kann gearbeitet werden und umso geringer ist der Treppeneffekt.
Außerdem kann es bei nachfolgender Wärmebehandlung von Bauteilen aus Stahl zu Härteverzug kommen, der beseitigt werden muss. Auch die Supportstrukturen müssen sauber entfernt werden. Eine spanende Finishbearbeitung ist somit unerlässlich. Bild 1 zeigt prinzipiell den Werkzeugbedarf für die mechanische Nachbearbeitung gedruckter Bauteile in Abhängigkeit von der gedruckten Qualität der Funktionsflächen. Der Werkzeugbedarf ist sehr groß. Lediglich in einem schmalen Bereich, in dem die Qualität der erzeugten Funktionsflächen bereits den finalen Anforderungen genügt, kann auf eine mechanische Nachbearbeitung verzichtet werden.
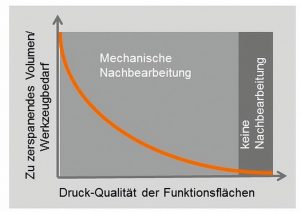
Kreativitätsschub für neue Produkte
LMT Tools fokussiert sich auf zwei Aktionsbereiche. Zum einen werden die Vorteile für die Werkzeugentwicklung selbst und für die Werkzeugfertigung genutzt, um neue Funktionen zu generieren und um den Anforderungen des Leichtbaus und der Ressourceneffizienz zu genügen. Zum anderen geht es um die Nachbearbeitung gedruckter Bauteile bei den Kunden. Dieser Fertigungsprozess stellt insbesondere in den Branchen Aerospace, Automotive oder auch in der Medizintechnik ganz besondere Anforderungen an die Zerspanung.
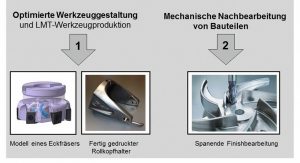
Begonnen wurde bei LMT Fette mit dem Druck von Rollkopfhaltern für die maschinenspezifische Anbindung von Gewinderollköpfen. Bild 3 zeigt prinzipiell die Gestaltungsstufen eines Rollkopfhalters beim 3D-Druck vom ursprünglichen konventionellen Design über die Topologieoptimierung und die funktionsgerechte 3D-Modellierung bis zum fertig gedruckten und voll funktionsfähigen Halter aus Stahl mit integrierter Kühlmittelzufuhr. Das Gewicht eines Rollkopfhalters konnte dabei um 43 % reduziert werden.
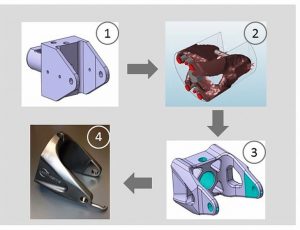
Als Beispiel für die einfache Gestaltung und Fertigung von Funktionsmustern kann ein Späneschutzcover für Rollköpfe genannt werden (Bild 4). Damit wird das Eindringen von Spänen, die in vor- oder nachgelagerten Dreh- oder Bohroperationen entstehen, in das grundsätzlich spanlos arbeitende Umformwerkzeug verhindert, beispielsweise beim Einsatz auf einer Revolvermaschine.
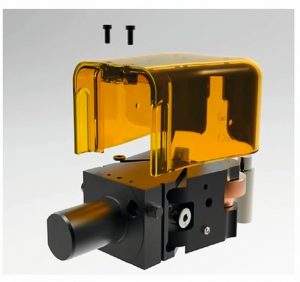
Problemlösungen zur Nachbearbeitung gefordert
Oftmals kann die Nachbearbeitung mit vorhandenen Werkzeugen geschehen, zum Beispiel mit dem sehr vielseitigen DHC-Schaftfräser von LMT Fette, der sich durch die ungleiche Drallsteigung und den besonders schwingungsarmen Lauf auszeichnet (Bild 5). Der wird bereits erfolgreich zur Finishbearbeitung gedruckter Knieprothesen in der Medizintechnik eingesetzt, insbesondere für das Unterteil (Tibia) der Prothese. Für das gewölbte Oberteil (Femur) gibt es spezielle Formfräser mit der zu erzeugenden Endkontur, mit denen die Bearbeitung höchst effizient erfolgt.
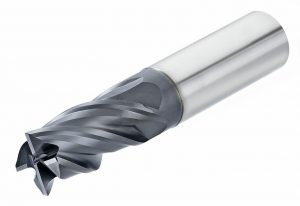
Das sind aber noch relativ überschaubare Lösungen. Wenn man sich etwas intensiver mit den Anforderungen der additiven Fertigung auf die mechanische Nachbearbeitung beschäftigt, wird alles wesentlich komplexer. Ein Stichwort ist „Form- und Lagetoleranzen“. In der konventionellen Fertigung auf einer CNC-Werkzeugmaschine sind die Werkstücke definiert eingespannt. Es existiert eine messtechnische Bezugsfläche oder Nullpunktdefinition als Basis für eine toleranzhaltige Komplettfertigung. Anders ist es bei den gedruckten Werkstücken.
Hier gibt es ein Problem mit der Nullpunktdefinition beim Umspannen des Werkstücks vom Drucker in die Fräsmaschine. Wenn das Teil zur Nachbearbeitung aus dem Drucker kommt, schwebt es sozusagen frei im Raum. Abhilfe bietet ein geeignetes Nullpunktspannsystem, das das Koordinatensystem beim Umspannen beibehält. Eine andere Lösung wäre die Komplettbearbeitung auf einer Hybridmaschine, auf der sowohl gedruckt als auch spanend bearbeitet werden kann.
Ein weiteres Stichwort ist „Eigenspannungen“. Zum Beispiel werden beim Fräsen einer Nute in konventionellem Stahl Eigenspannungen frei, die zur Deformation der Wandungen führen können. Zur Kompensation werden die Werkzeugschneiden entsprechend gestaltet. Diese Korrektur sieht für gedruckte Werkstoffe anders aus, weil deren Mikrostruktur eine andere ist und weil sich damit auch die gewählte Wärmebehandlungsroute auf das Spannungsverhalten auswirkt.
Werkstoffgefüge und Wärmebehandlung gedruckter Bauteile haben darüber hinaus Einfluss auf die Werkzeugleistung und die Standzeit. Die Schneidengeometrie und die Schnittwerte müssen entsprechend optimiert werden.
Es gibt zahlreiche mechanische Fertigungsverfahren, die (noch) nicht durch die additive Fertigung substituiert werden können. Dazu gehört natürlich das Fräsen zur Nachbearbeitung der gedruckten Teile, wie bereits beschrieben. Darüber hinaus wird die Erzeugung von Passbohrungen durch Ausspindeln oder Reiben voraussichtlich nicht substituierbar sein. Zu nennen ist auch die spanlose Außen- und Innengewindeherstellung durch Gewinderollen beziehungsweise Gewindeformen. Hierbei kommt es besonders auf die durch den Umformprozess bedingte Verdichtung der Materialfasern im Gewindegrund an, wodurch die sehr hohe Gewindefestigkeit erreicht wird.
Auch für die Substitution des Gewindebohrens durch Drucken besteht noch Entwicklungsbedarf. Die Qualität eines gedruckten Gewindes ist nicht vergleichbar mit einem spanend hergestellten und es muss nachgeschnitten werden. Trotzdem können noch Steigungsfehler auftreten. Lediglich die Kernlochbohrung kann additiv hergestellt werden. Das Gewinde selbst muss dann nach wie vor mit einem Gewindebohrer gefertigt werden.
Generell sind die additiven Verfahren bis dato für die Einzelfertigung oder bestenfalls für kleinere Losgrößen wirtschaftlich anwendbar, weil die Auftragsraten noch zu gering bzw. die Schichtdicken zu groß sind. Die Druckzeiten sind zu lang und steigen mit abnehmender Schichtdicke weiter an. Für die Massenfertigung werden somit absehbar die konventionellen Verfahren, beispielsweise auch das Wälzfräsen, ihre effiziente Berechtigung behalten.
Der Kreativität
der Konstrukteure und auch der Fertigungstechniker sind keine Grenzen gesetzt. Von ihnen wird ein komplett neues 3D-Druck-Denken gefordert. Viele bereits bestehende Produkte müssen neu konstruiert werden.